Thursday 9th May 2024
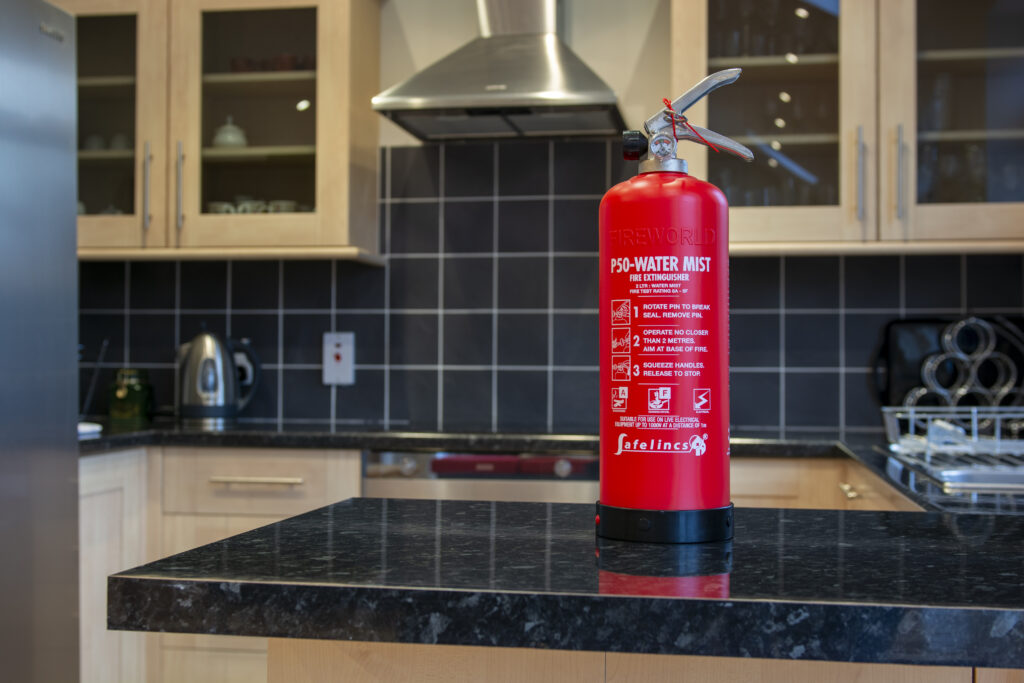
HMO’s (‘homes of multiple occupancy’) are rented properties with shared communal spaces, like kitchens and bathrooms, where the tenants lease independently. A common example of this is student housing, while HMOs are often habituated by recent graduates, and other young people. Shared communal spaces often have neglected responsibility for safety and general housekeeping, meaning that the risk of fires in HMOs is raised.
The Responsible Person for the building has a duty to maintain and promote fire safety in rental properties. This includes installing the right fire detection systems, educating tenants on fire safety, and maintaining fire doors. In the event of a fire, domestic firefighting equipment can be a lifeline for tenants.
Should landlords provide fire extinguishers in HMOs?
At least one suitable fire extinguisher must be provided in every kitchen of a large HMO (more than 5 tenants). Water Mist extinguishers are ideal for this, as they can be used on solid and liquid combustible fires, as well as small cooking fires. This covers most home fire risks. The landlord, or Responsible Person for the property must ensure that all extinguishers are well maintained. They must also be serviced annually (if applicable), and replaced if used or damaged.
Fire extinguishers can be used to aid a tenant in safe escape from a building. They may also be used to tackle small flames before they become out of control.
In private rentals, landlords are not obliged to provide fire extinguishers, although it is recommended.
Should landlords provide fire blankets in HMOs?
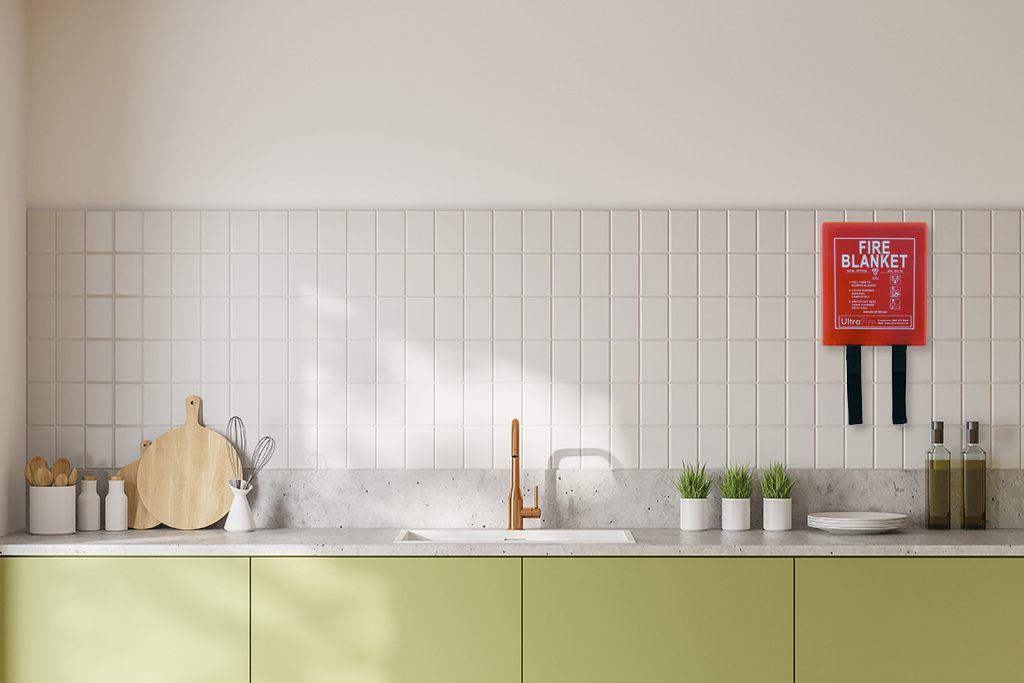
Landlords must provide one fire blanket per kitchen in every HMO, no matter how many tenants are resident. These should be hung on a wall away from the likely source of fire (cooker), regularly checked, and replaced if used or damaged. Fire blankets provide a simple and effective solution to frying pan fires, which cannot be extinguished with water. Accidents in the kitchen which cause fires can be devastating if allowed to spread.
The provision of fire blankets in private rentals is not mandated. However, more than half of all UK house fires start in the kitchen. Installing a fire blanket protects both the tenant and the property from fire.
Are tenants expected to fight fires?
Tenants cannot be expected to put themselves at risk to fight a fire. By providing fire fighting equipment, such as extinguishers and fire blankets, the tenant is provided with the option to tackle a small fire before it spreads, and only if it is safe to do so.
When a new tenant moves in, they should be provided with guidance about what to do in a fire. This includes instruction on how to use fire-fighting equipment if it has been installed, but only to attempt this if it is safe. More importantly, tenants should be told how to raise the alarm in the event of a fire, and how to safely evacuate the building. This is particularly important in flats and HMOs.
Misuse of fire extinguishers in HMOs
Educating tenants on the correct use of the extinguishers installed in HMOs is essential; getting this wrong can be fatal. Where more than one type of fire extinguisher is installed to cover different fire risks, there is a risk of the wrong type being used. This can be incredibly dangerous, not only because the extinguisher will not work, but because it could make the fire worse, and spread the flames. The only way to avoid this is to install one type of extinguisher. However, this extinguisher must be suitable for all present fire risks. A Water Mist extinguisher is therefore a good example of a versatile extinguisher that provides good all round coverage for most common risks.
There is also, of course, a risk of vandalism to and with fire extinguishers in HMOs. This could involve damage to the extinguisher, or unnecessary deployment of the extinguisher. The best way to avoid this is educating residents on the importance of extinguishers for fighting fires. This is particularly important as if there are repeated incidents of vandalism, the risk assessment may find the risk of this to outweigh the risk of fire. In this case, extinguishers would need to be removed, meaning that they would not be available in a fire.
Installing Water Mist extinguishers overcomes some of the dangers associated with accidental or unnecessary deployment. These units contain only deionised water, which is non-toxic, and will not cause damage to furniture or property.
How can landlords prevent the spread of fires?
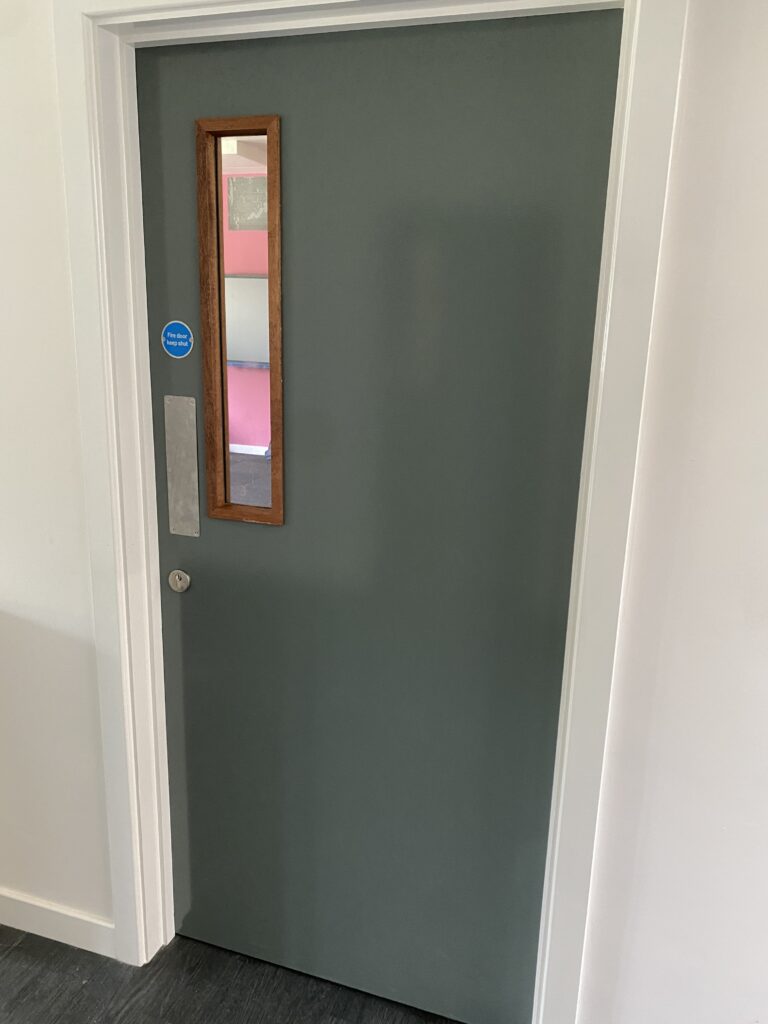
Fire fighting is a last resort in stopping the spread of fires. Tenants and the properties they live in must be primarily protected by preventative measures. This includes:
- Maintenance of fire doors – use our free fire door inspection checklist to monitor the condition of fire doors in HMOs. From January 2023, in buildings over 11m in height, flat entrance door must be checked annually, while doors in and entering onto communal spaces must be checked quarterly. This includes checking door closers for vandalism – appropriate action must be taken where these have been deactivated due to tenants with mobility issues struggling with heavy fire doors.
- Fire detection systems – Every HMO must have a suitable fire detection system, which is maintained and tested regularly.
- Educating tenants – when they move in, tenants should be given guidance about good house keeping in relation to fire safety. They should also be advised on how to respond to a fire, including how to raise the alarm and evacuate.
- Fire suppression systems – in some buildings, such as blocks of flats, suppression systems like sprinklers may be appropriate. Sprinklers reduce the damage caused by fire, and to allow tenants time to escape.
- Fire-fighting equipment – fire blankets must be installed in the kitchens of all HMOs, and tenants should be advised on how and when to use them. Similarly, where fire extinguishers are installed, tenants should be given guidance on when they might attempt to use them, and which type of extinguisher to use.
Are tenants liable for fires?
There are over 30,000 house fires in the UK every year. These accidents are often devastating for the residents, who may lose all of their belongings. Landlords’ building insurance is therefore essential for the protection of their property from fire.
Tenants cannot be held accountable for failing to fight a fire that breaks out in their home. However, they may be liable for causing the fire if the subsequent investigation finds them to have been at fault. Tenants should therefore invest in contents insurance, including fire damage caused by accidents, faulty appliances, electrical issues.
It is Responsible Person’s duty to ensure that fire, and the damage they cause, are prevented in their property. This can be done primarily through education of tenants. Further to this, the maintenance of fire doors, fire detection systems, fire blankets, and fire suppression systems reduce the damage caused by fires. In large HMOs, or if the risk assessment deems it appropriate, install extinguishers for the control of small fires, or to assist tenants in safe escape from the building.