Gas Suppression Servicing and Maintenance
What is a Gas Fire Suppression System?
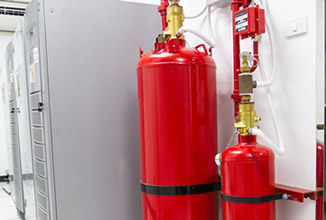
A gas fire suppression system is typically utilised in areas where electrical equipment such as website servers and hosting equipment is operating or being stored. The IT, Data and Communication sector utilise sensitive electrical equipment where traditional methods of extinguishing fire (water or foam) could cause extensive damage to the equipment. A well-engineered gas suppression system means that water is not always essential to contain fires.
Gas suppression systems are designed to extinguish fires by reducing the oxygen content to a level where most materials will no longer burn (below 15%) which means they are generally seen in areas that have little foot traffic - however life is sustainable at these levels, and healthy people would not notice any adverse effects, so they can also be utilised in some occupied areas. Typically activated by a smoke detection system, a gas suppression system will utilise one of a number of different clean / environmentally friendly suppressants:
- Proinert
- IG541 / Inergen (A blend of Nitrogen, Argon and CO2)
- IG55 / Argonite (A blend of Argon and Nitrogen - provides higher levels of gas suppression for longer)
In addition to the above, there are also systems that utilise synthetic agents to create a clean chemical gas which functions by absorbing heat, rather than oxygen. Previously Halon was the most popular chemical gas, but due to troubles with ozone depletion, it was removed from commercial use. A replacement for Halon was therefore required, and so a number of clean chemical gases were developed which have zero ozone depletion potential. These gases include:
- FM200 / HFC227
- Novec 1230
All of the above gases are safe for use on electrical fires, making them ideal for server rooms, data centres, stores, and archives. These systems also have minimal storage requirements as they utilise small quantities of gas in pressurised cylinders. Due to the susceptibility that gas has to escape, it is important that is completed when a system is first commissioned, and at least once annually following installation, to ensure that the room where this system is installed is adequately sealed. A room that is inadequately sealed can allow the fire suppression agent to dissipate too quickly before it has time to cool or extinguish the fire. However, if a room is sealed too tightly, the fire suppressant can cause internal structural damage to the enclosure if activated, therefore making this regular testing essential.
Gas suppression is recommended for biannual maintenance (twice a year). It is also important to note that gas cylinders require replacement / service exchange when they are 10 years old. This is carried out because the cylinders which are used to hold the agent or gas are pressurised, and under EU requirements, all pressure vessels must be tested at least every 10 years to ensure they are still safe to use.
What is typically included in a Servicing and Maintenance Package?
Certain elements should be included in all servicing and maintenance packages for gas fire suppression systems. These elements are in place to give you the confidence that your system has been serviced properly, by someone who is qualified, and that it has been completed to a recognised industry standard.
- Visit by a BAFE certified gas suppression engineer
- A Room Integrity Test (RIT), and complete inspection of your suppression system and all associated components
- A functional inspection of your fire alarm panel, detectors and sounders
- All servicing and maintenance works carried out in accordance with BS EN 15004 and BS 5839-1
- Comprehensive report and diagnosis of any issues that may require remedial work
What usually happens during the servicing and maintenance on a Gas Suppression System?
Assuming that the Room Integrity Test (RIT) has already been completed, during a regular site visit a trained engineer will carry out checks of all components to ensure that your system is fit for purpose and will operate as intended in an emergency. Regular servicing and maintenance is critical to the longevity of suppression systems to ensure that all components are free from wear or damage. You can expect the following to take place during a site visit:
Mechanical Checks
- Check pipes and fittings are to the correct standard, and supports have been fitted at the correct intervals
- Check nozzles are fitted in accordance with the design requirements, have been aligned correctly, and that the orifice area corresponds to the approved installation drawing
- Check all pipes and nozzles are adequately braced against the reaction of a discharge
- Check pipework has been painted and / or properly identified
Cylinder Checks
- Check containers are free from mechanical damage, corrosion and tampering, and are fitted with appropriate instruction plates
- Check container racking and brackets are complete, and all fixing links are appropriately fitted
- Check pressure gauges to ensure fill is correct, and check the dates of each cylinder to ensure they are not more than 10 years old
- Where gauges are not fitted - weigh or liquid level check the cylinders
- Remove actuators and check operation of mechanical devices, and correct fitting of electric devices / pressure monitoring devices (where fitted)
Electrical Checks
Firstly, inspect the fire alarm log book, and ensure the appropriate action is taken with regards to outstanding faults / defects. Remove all solenoids / electrical actuators to ensure that the system is not accidently activated during servicing and maintenance works. The following tests and checks will then be conducted:
- Carry out checks on all power supplies and battery chargers, ensuring that they are free from damage, and are in good health
- Check the charge voltage of connected batteries (and adjust if required)
- Test batteries according to the manufacturer's recommendations
- Check Specific Gravity (SG) of each cell, top up electrolyte, and ensure battery terminals are greased
- Check the panel PSU / charger under full alarm load (with batteries disconnected)
- Carry out checks at all control panels and repeated panels
- Check all visual and audible indicators and ensure all display panels can be clearly read
- Check operation of all control buttons and switches, and security of all terminations and fuse carriers
- Similarly a fault condition for all monitored circuits, and check that a maintenance label is fitted
- Check function of ancillary functions, cause and effects programming, and signal strength (for wireless systems)
- Check all fire indication zones for correct alarm mode operation
- Carry out checks on all field operating devices
- Check all fire detectors have not been damaged or tampered with, and record in the log book which devices have been tested
- Test point smoke, point heat, optical beam, CO fire, and flame detectors using appropriate methods to produce a fire alarm signal
- Check operation of alarm warning devices and ensure they are clean and undamaged (bells, sounders and strobes)
- Check (if available) the analogue values / contamination log of the field devices to ensure they are within the manufacturer's limits
- Check and test the switch mechanism on a manual call point
- Test the link to the Alarm Receiving Centre (ARC) to confirm the correct signal was received
Visual Checks
Carry out visual inspections to verify whether:
- All manual call points are unobstructed and visible, and all accessible cable and fixings are appropriate
- Any new exits have been created and are properly accounted for
- Any new / relocated partitions have been erected within 500mm of any automatic fire detector
- Any storage encroaches within 300mm of ceilings
- A clear space of 500mm is maintained below each automatic fire detector
- Any changes to the use of areas which would make the existing types of fire detector unsuitable
- Any building alterations / extensions require additional fire detection equipment
- Check that any solenoids / actuators are not 'active'
Final Reporting
- Complete service and test certificate, noting any remedial actions where required
- Reinstate system upon completion of service, and record test and service date on equipment
What questions will I be asked before servicing and maintenance can take place?
- What type of gas is used in the system?
- How many cylinders are in the system?
- Are you able to provide an image of the existing system?
- Are there any known faults or issues?
- Has the system been maintained before?
- Has a Room Integrity Test been completed in the last 12 months (this is an annual requirement)?
- Are there any access restrictions or requirement for permits to work?
- Are you able to provide the last maintenance certificate for review? (if applicable)
Reviewed: 22/12/2022 (doc:759 V1.0). Our articles are reviewed regularly. However, any changes made to standards or legislation following the review date will not have been considered. Please note that we provide abridged, easy-to-understand guidance. To make detailed decisions about your fire safety provisions, you might require further advice or need to consult the full standards and legislation.